Hot Axle Box & Hot Wheel Detector
(HABD & HWD)
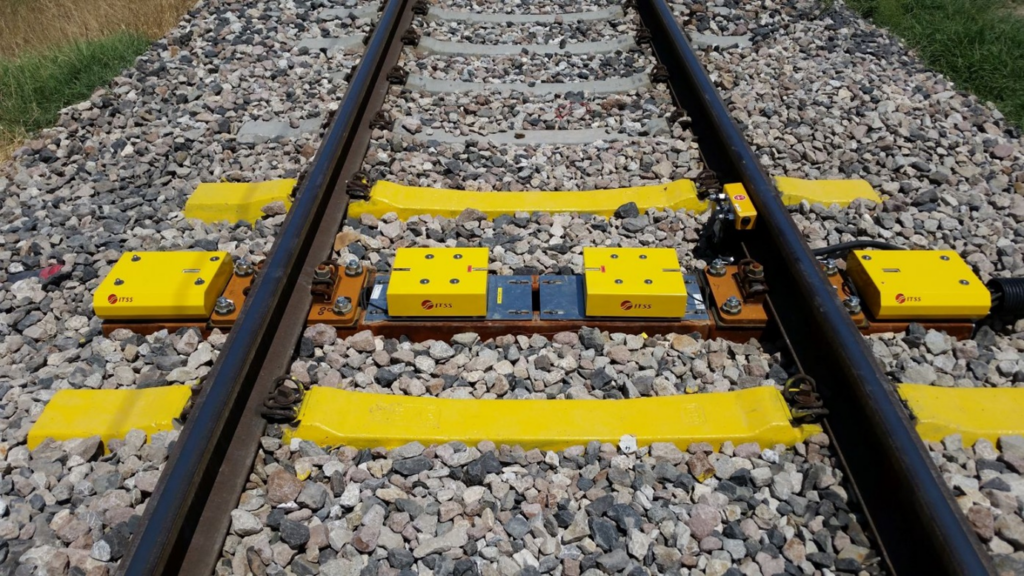
Overview
Greater train speeds, greater axle loads, as well as the use of different coach types, demand innovative systems. ITSS has developed Pegasus, a system which meets the highest safety standards and, at the same time, takes into account the pressure of cost under which railway operators work today.
The Pegasus System identifies and records all standard axle types and braking systems. It detects hot bearing boxes and defective brakes with high reliability and the key to the impressive price-performance ratio of our Pegasus system is its modular design. There are 10 beam scanners scanning all standard axle-bearing types over a maximum width of 140mm, capable of detecting any hazardous conditions. Also, state-of-the-art infrared and digital technology ensure the rapid and precise processing of the measured values.
The PEGASUS hot-box detector is the only system on the market equipped with a special VIBRATION SENSOR. This sensor measures the influence of the vibration caused by the train on the system. This vibration can potentially cause gradual damage that can go unnoticed to the system. The damage becomes evident only when the system fails because it has been destroyed. However, if the influence of the vibration is monitored, then timely intervention will prevent premature damage to the system. Important: this use of a vibration sensor for hot-box detection has a European patent. This unique function is protected by a European patent (EP 1772342)
The operating system used by PEGASUS is LINUX which is more reliable and less susceptible to viruses than the Windows operating system
PEGASUS is the only system on the market which offers scanning facilities using up to 10 beams (extending 8-beam scanning to 10-beams is an option which only ITSS offers at this time – other systems usually offer only 4 or a maximum of 8-beam scanning)
Pegasus identifies and records all standard axle types and braking systems. Hot bearing boxes and defective brakes are reliably detected
Automatic identification of locomotives, coaches, and train compositions.
Technical Data
General technical data:
Linux OS
IVM vibration protection and threshold monitoring (Patent EP 1772342)
Measuring of all Standard axle bearing types
Entire bearing surface is continuously measured
Higher safety due to redundant sensing, using up to 10 independent beams
3-D thermal image recorded with ca. 7200 scanned points at 500 km/h
According to the norm: TSI Interoperability of the trans European high-speed rail System Directive 2006/860/CE
EN 55011:98 + A 1:99 + A2:02, Class B (Emissions Test)
EN 50121-4:00 (EMC).
EN 50125-3
Development according to EN50128
Modular system design
Sensor modules can be replaced in a few minutes
No adjusting needed after replacing
Tamping without de-installing the system components
Scanner link Ethernet 100MB
Scanner versions 4/8/10 Beams
Up to 32 HBD/HWD Scanner to be connected to only one track side electronic system
Maximum number of axles: 3000
Data link Format TCP/IP, several protocols ( XML, OPC etc.)
Automatic identification of locomotives, wagons and train compositions
HABD Hot axle box detector:
Thermal imaging of axle bearings
Max. train speed: 500 km/h
Thermal imaging temperature range: 0°C – 200°C
Temperature resolution: +/ – 1°C
Accuracy (repeated measurements): +/ – 1° C
Sensor width:
60 – 140mm (10 beams)
50-120mm ( 8 beams)
25-60mm 4 beams
Redundant Auto calibration (RAC) and self control
Effective range: -40°C till +70°C
Scans all kind of axle bearings
HWD Hot wheel detector:
Thermal imaging of brakes
Max. train speed: 500 km/h
Thermal imaging temperature range: 50°C – 650°C
Temperature resolution: +/ – 1°C
Accuracy (repeated measurements): +/ -10° C
Sensor width for rim and disc brakes: 50 – 140 mm
Redundant Auto calibration (RAC) and self control
Effective range: -40°C till +70°C
Scans disc and rim brakes